Plastic dosing 4.0 becomes a reality
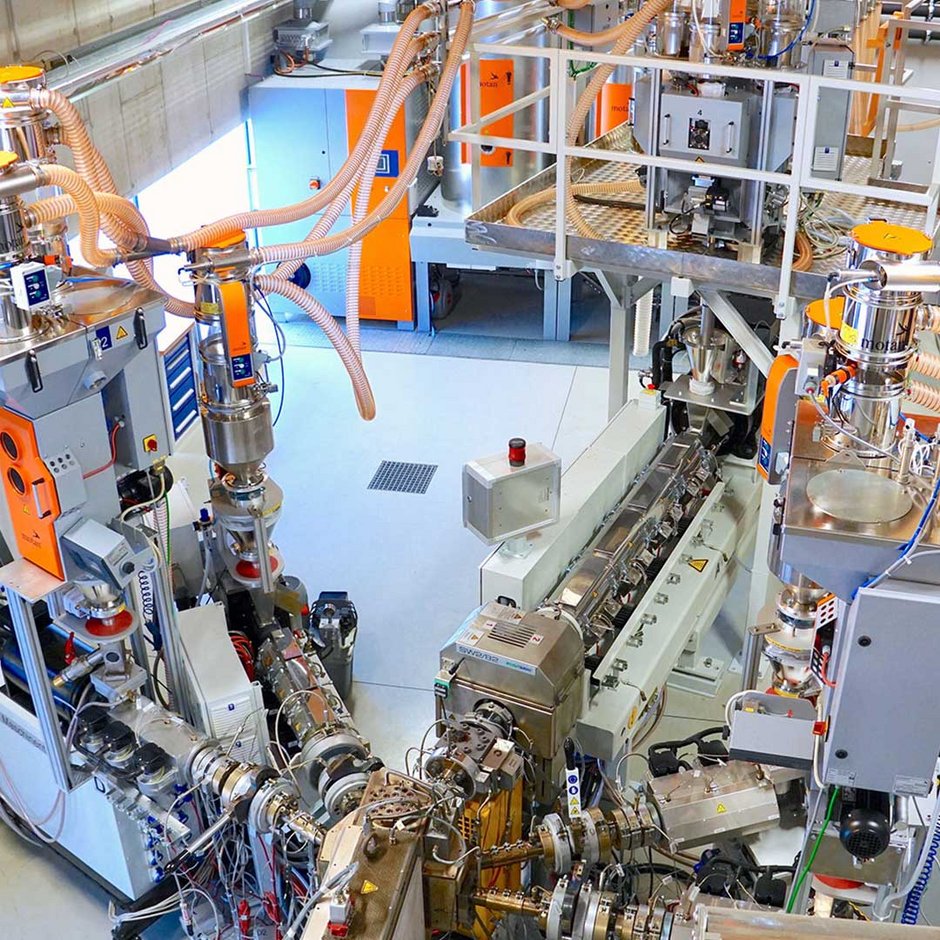
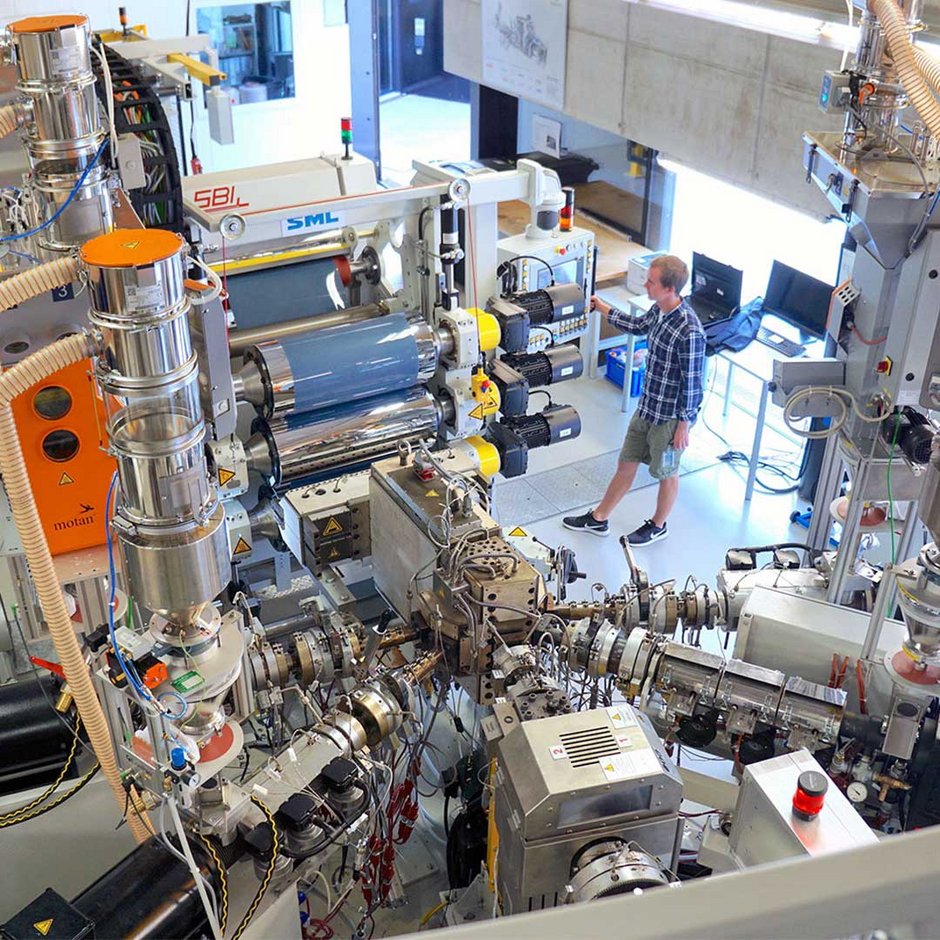
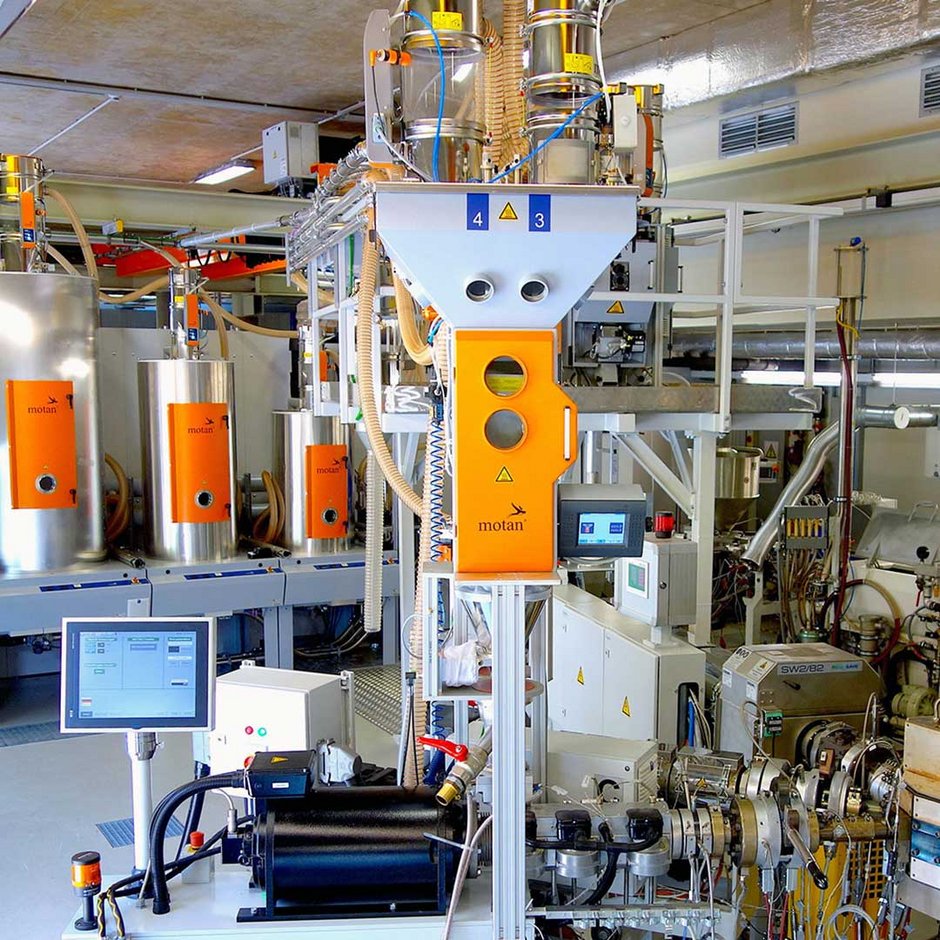
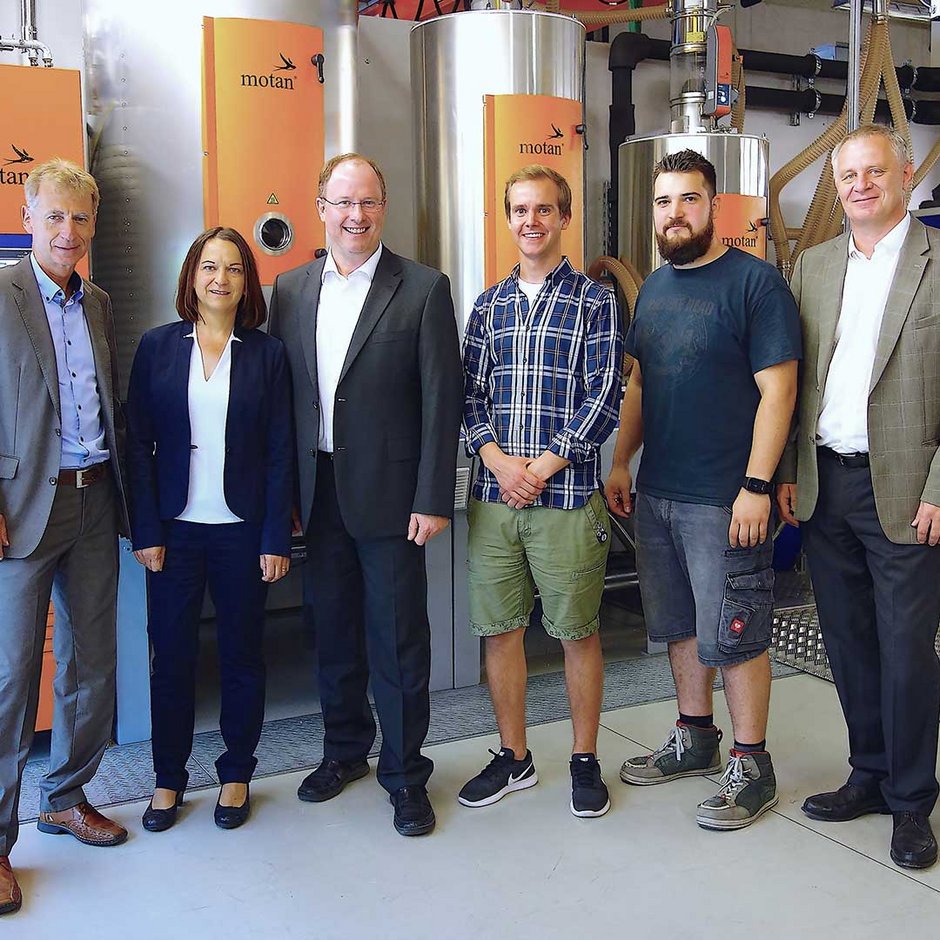
Fully automated process control for all components of extrusion systems is the top priority at the Institute for Polymer Extrusion and Compounding (IPEC) at Johannes Kepler University (JKU) in Linz on the Danube.
Necessary control algorithms for this are developed together with industrial partners and other JKU institutes from the fields of mechatronics and computer science. The development platform is a 9-layer extrusion system on an industrial scale. motan is one of the partners involved. The goal of this cooperation is to develop an easy-to-use control system, in which all components communicate and automatically coordinate with each other according to Industry 4.0 standards.
Finding the ideal operating point of an extrusion system is still a demanding task for the machine operator, despite the wide range of possibilities available in sensor and measurement technology, data processing and control engineering. Particularly then, when – depending on the base machine – the operating points of such different infrastructure systems have to be changed. Even more so when products are changed frequently under time pressure.
This is where researchers, technicians and students of the IPEC at JKU in Linz come in. Prof. Dr. Jürgen Miethlinger states: “Our vision is the self-optimizing overall system, which takes all plant components to the new operating point during a product change and then continuously coordinates and optimizes them during operation. The prerequisite for this is to have a precise image of the current production situation. To do this, we record measurement signals from all system components every millisecond. Our “Big Data”- specialists structure this data, which represents the digital reality of the theoretical physical processes.
At the end of the project
At the end of the project, we will receive a complete digital image of the entire facility including all infrastructure systems. Our goal is to operate the actual digital machine as a process simulator and to supplement it with self-learning capability. New operating states can thus be simulated and optimized in detail in advance, including control algorithms for ongoing operation of the system. Long product changeovers and startup times will be a thing of the past, which will make the operation of extrusion systems more flexible. An important prerequisite for our success is that we fully succeed in integrating the processes of infrastructure devices into the operation of the base system.”
Optimal sub-processes result in an optimal overall process
One of our sub-projects is to study the role of gravimetric dosing of both minimum and maximum quantities. The significance of this aspect is made clear when looking at the specification of a 1mm thick 7-layer barrier film. The central layer of high-quality barrier material is only 50 μm thick (= 5% material content). Above are two 25 μm thick bonding agents, and two 350 μm thick layers of structural material, e.g. recycled material, and one 100 μm thick cover layer. To achieve a consistent layer thickness, consistent dosing of the material conveying is the most important factor.
The fact that motan devices were able to meet the expectations of JKU researchers was the technical basis for concluding the partnership agreement with IPEC / JKU. The next step will be to transfer this partnership to the future factory on the university campus currently under construction: The LIT Factory. It will be used to operate extrusion and injection molding at Industry 4.0 level.