Dosaggio della plastica 4.0 diventa realtà
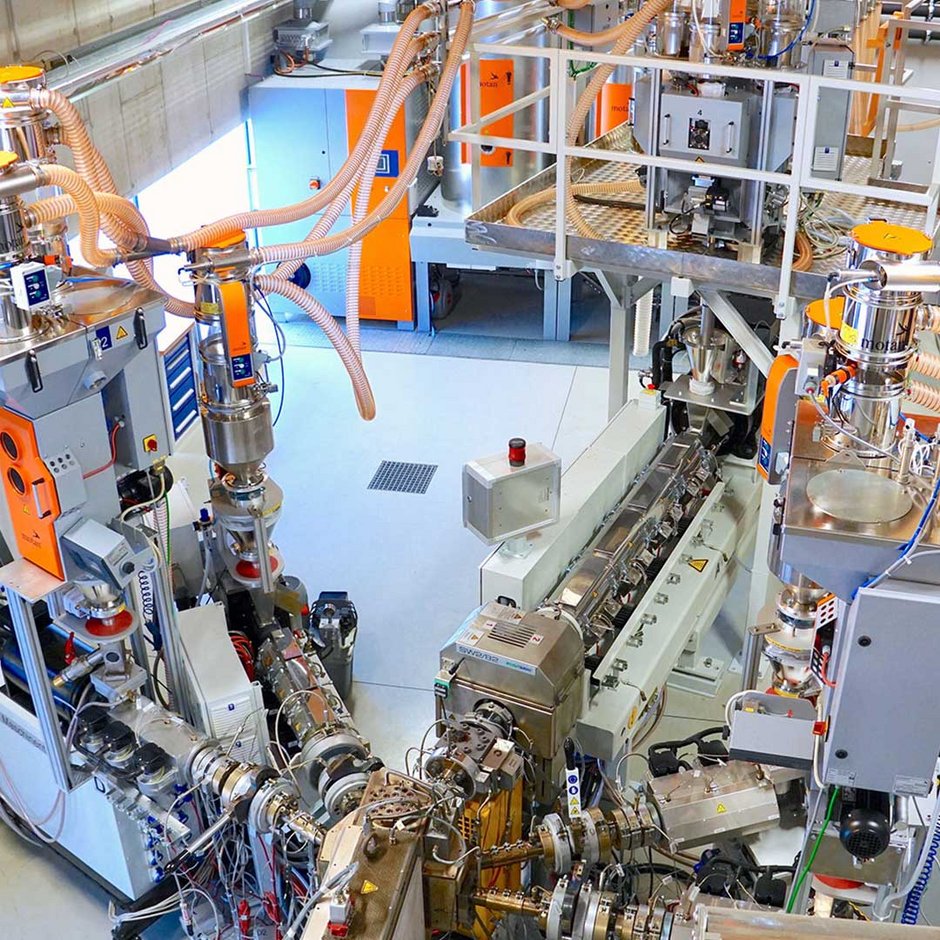
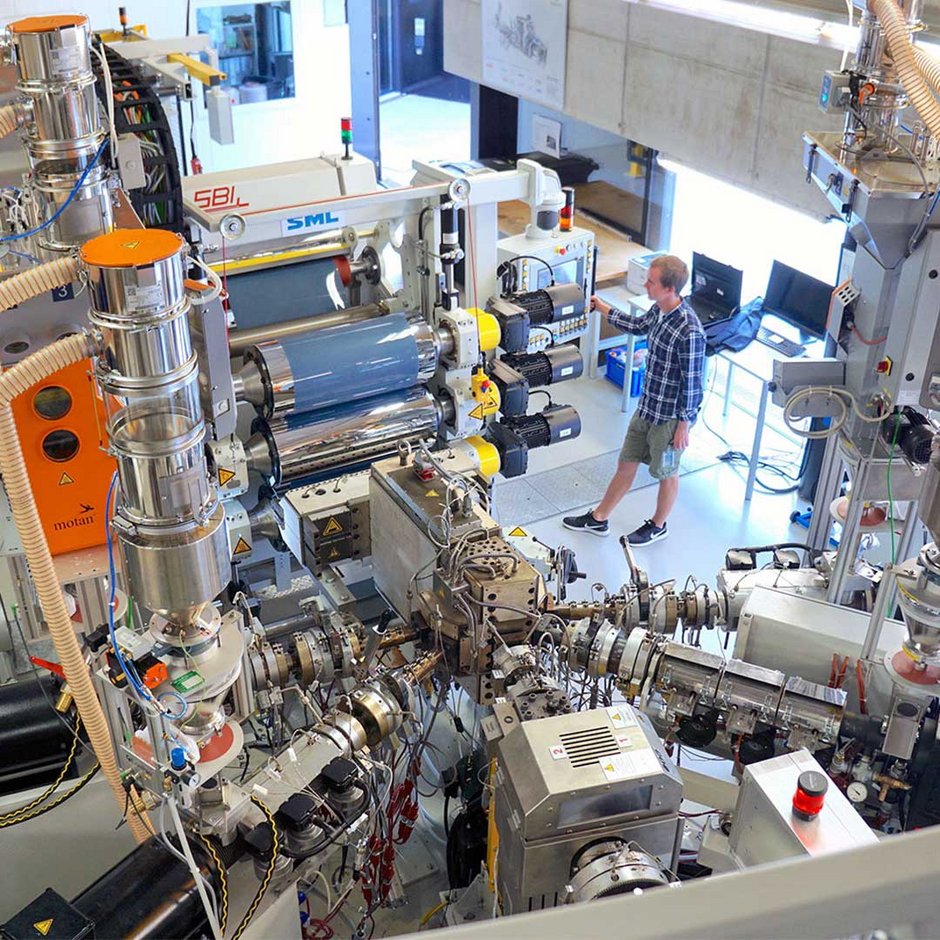
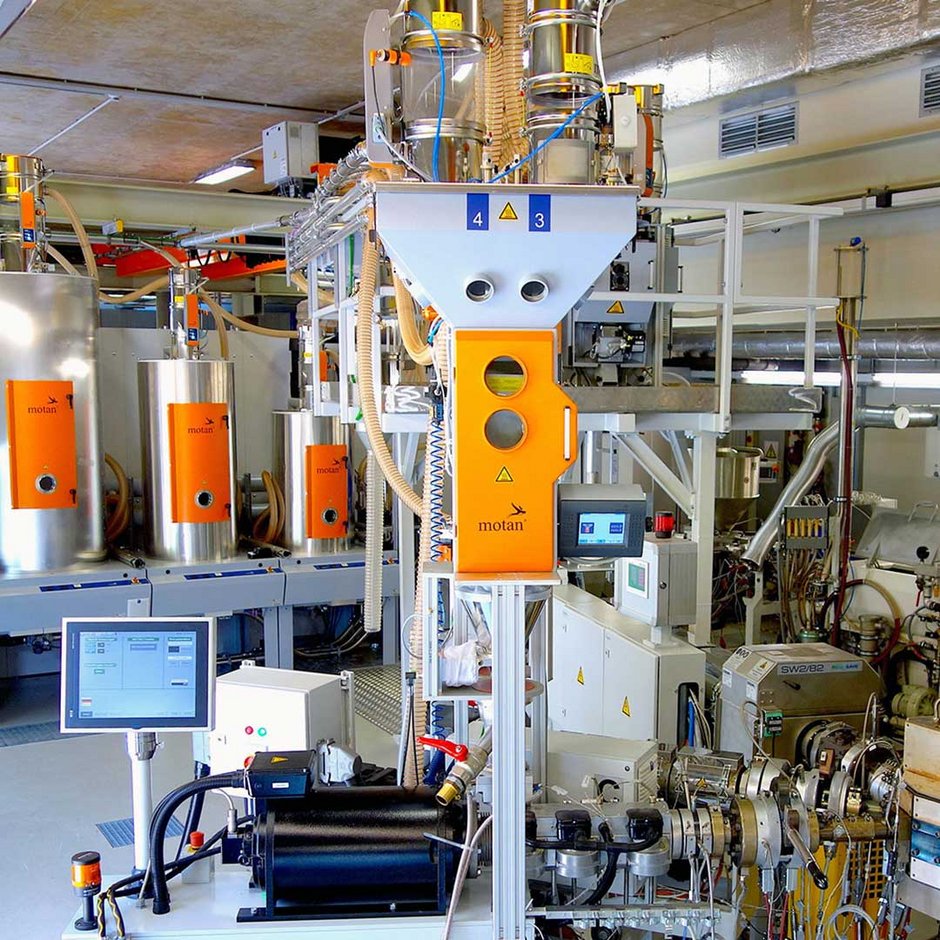
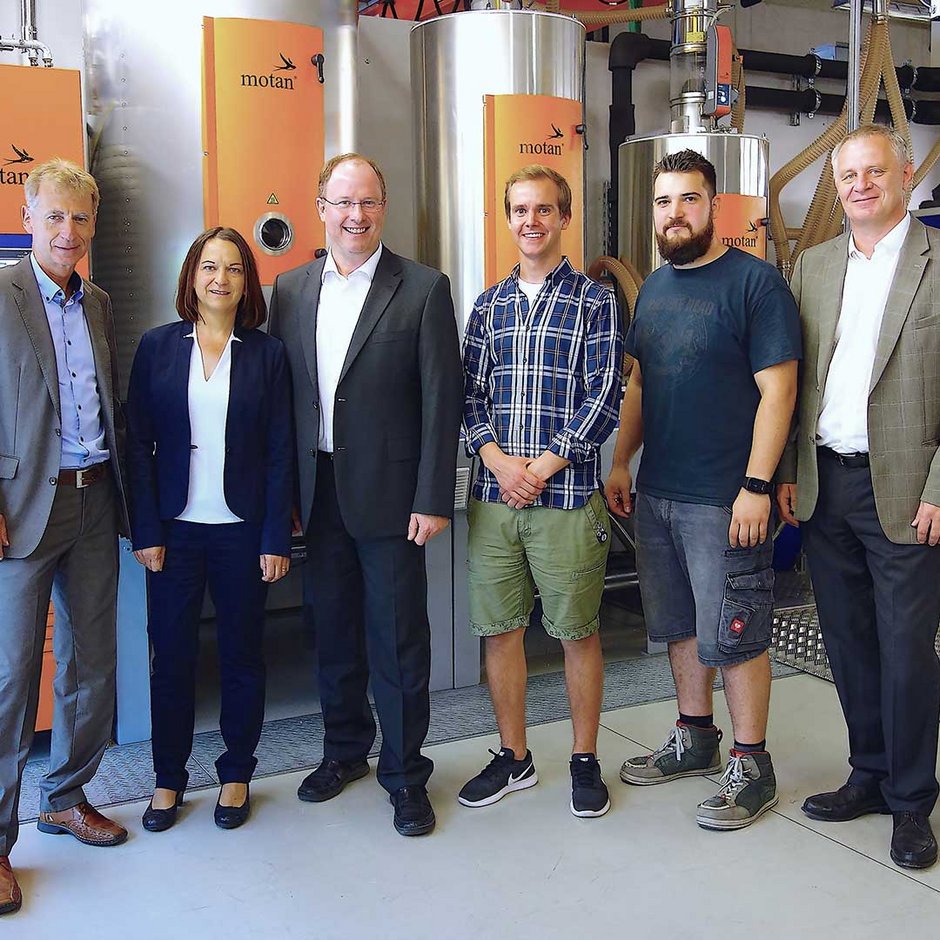
Priorità assoluta in agenda dell’Istituto di estrusione e compositi dei polimeri (IPEC) dell’Università Johannes-Kepler (JKU) di Linz sul Danubio è realizzare un sistema di processo completamente automatizzato per tutte le componenti di impianti di estrusione.
I necessari algoritmi di controllo vengono sviluppati in collaborazione con partner industriali e altri istituti della JKU attivi nei settori della meccatronica e dell’informatica. La piattaforma di sviluppo è un impianto di estrusione a 9 strati su scala industriale. motan è uno dei partner coinvolti. Obiettivo della collaborazione è sviluppare un sistema di controllo degli impianti facile da usare, in cui tutti i componenti comunichino tra loro e si coordinino automaticamente secondo gli standard di Industria 4.0.
Nonostante le ormai varie possibilità disponibili nella tecnologia dei sensori e di misurazione, nell’elaborazione dei dati e nella tecnologia di controllo, trovare il punto di lavoro ottimale di un impianto di estrusione, per l’operatore della macchina ciò è ancora un compito impegnativo. In particolare, quando, in funzione della macchina base, è necessario modificare anche i punti operativi di sistemi infrastrutturali così diversi, come ad es. gli impianti di trasporto e dosaggio del materiale. Tanto più quando i prodotti devono essere cambiati frequentemente con poco tempo a disposizione.
È qui che entrano in gioco i ricercatori, i tecnici e gli studenti dell’IPEC dell’università JKU di Linz. Il professore universitario Jürgen Miethlinger afferma: «La nostra visione è un sistema globale auto-ottimizzante, che “porta” tutti i componenti dell’impianto al nuovo punto operativo durante un cambio prodotto e poi li coordina e li ottimizza continuamente durante il funzionamento in corso. Presupposto di ciò, è quello di disporre di un quadro preciso della situazione attuale della produzione. A questo scopo rileviamo i segnali di misura di tutti i componenti dell’impianto ogni millisecondo. I nostri specialisti “Big Data” strutturano questi dati, che rappresentano la realtà digitale dei processi fisici teorici.
Al termine del progetto
Al termine del progetto riceviamo un’immagine digitale completa dell’intero impianto, compresi tutti i sistemi infrastrutturali. Il nostro obiettivo è quello di utilizzare la macchina reale digitale come simulatore di processo e di integrarla con una capacità di autoapprendimento. In questo modo è possibile simulare e ottimizzare dettagliatamente in anticipo nuovi stati operativi nonché gli algoritmi di controllo per il funzionamento in corso del sistema. I lunghi tempi di cambio prodotto e le fasi di avviamento saranno un ricordo del passato, il che faciliterà l’utilizzo flessibile degli impianti di estrusione. Un presupposto importante per il successo della ricerca è riuscire a integrare pienamente i processi delle apparecchiature infrastrutturali nel ciclo operativo dell’impianto di base.»
Processo complessivo ottimale grazie a processi parziali ottimali
Un progetto parziale nell’insieme è studiare il ruolo del dosaggio gravimetrico sia per le quantità minime che quelle massime. L’importanza di questo aspetto parziale è chiaro se, in modo esemplificativo, si considera la specifica di una pellicola di barriera a 7 strati dello spessore di 1 mm. Il suo strato centrale di materiale barriera d’alta qualità ha uno spessore di 50 μm (= 5% quota di materiale). Sopra di questo si trovano due agenti di accoppiamento (collanti), ciascuno dello spessore di 25 μm, e due strati di materiale strutturale dello spessore di 350 μm, ad es. materiale riciclato e uno strato di copertura dello spessore di 100 μm ciascuno. Per ottenere uno spessore uniforme dello strato, il dosaggio costante del materiale trasportato è il fattore più importante.
Il fatto che le apparecchiature motan siano state in grado di soddisfare le aspettative dei ricercatori della JKU è stata la base tecnica per stipulare un contratto di partnership con IPEC/JKU. In una fase successiva, la partnership sarà trasferita anche al futuro stabilimento in costruzione sul campus universitario: la LIT Factory. L’estrusione e la pressofusione saranno effettuate a livello di Industria 4.0.