Kunststoffdosierung 4.0 wird konkret
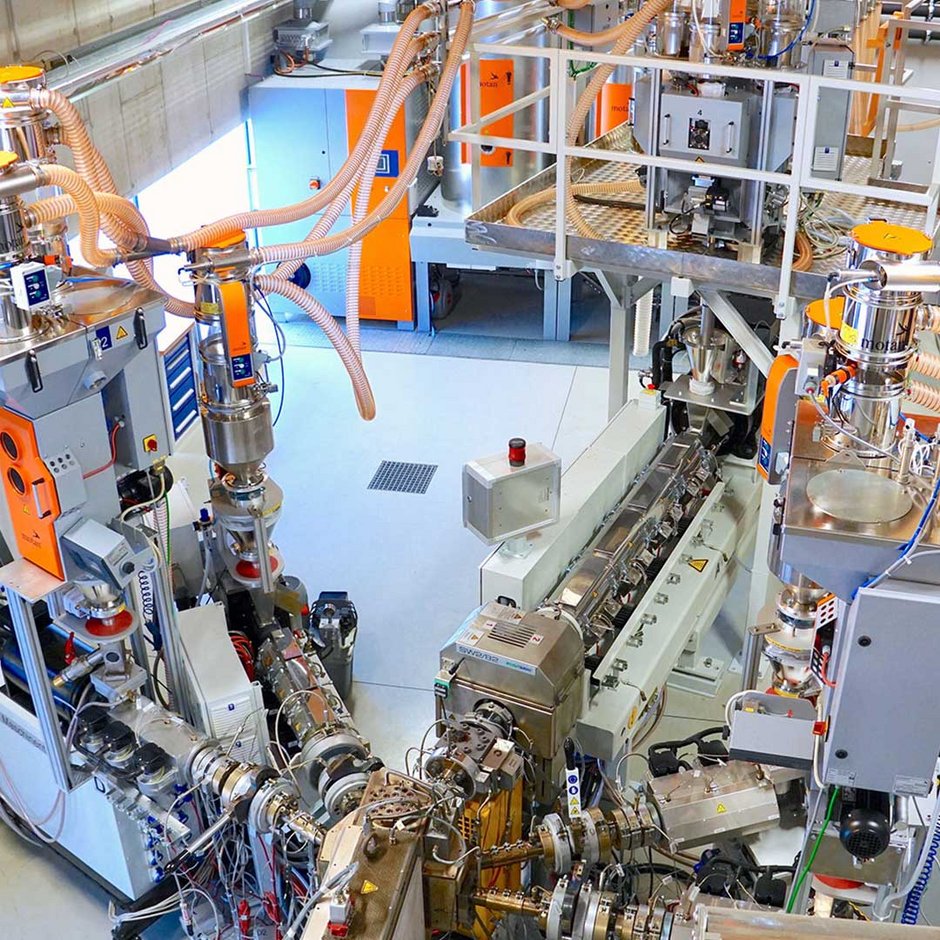
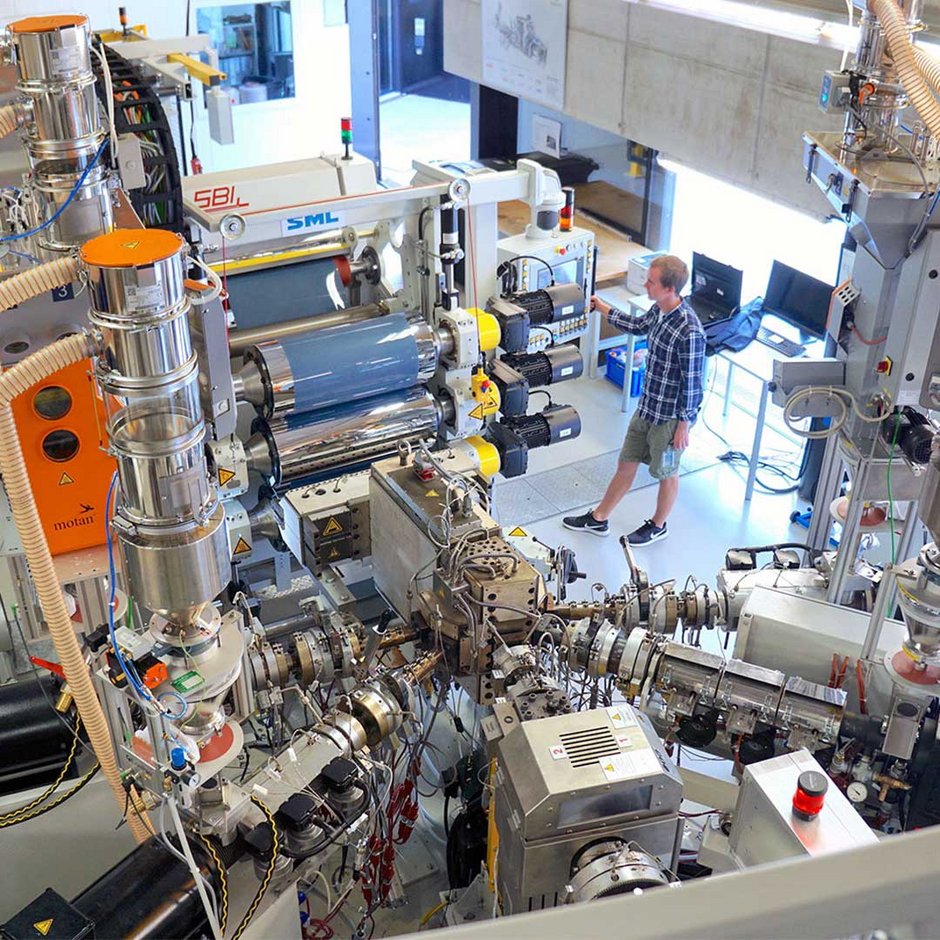
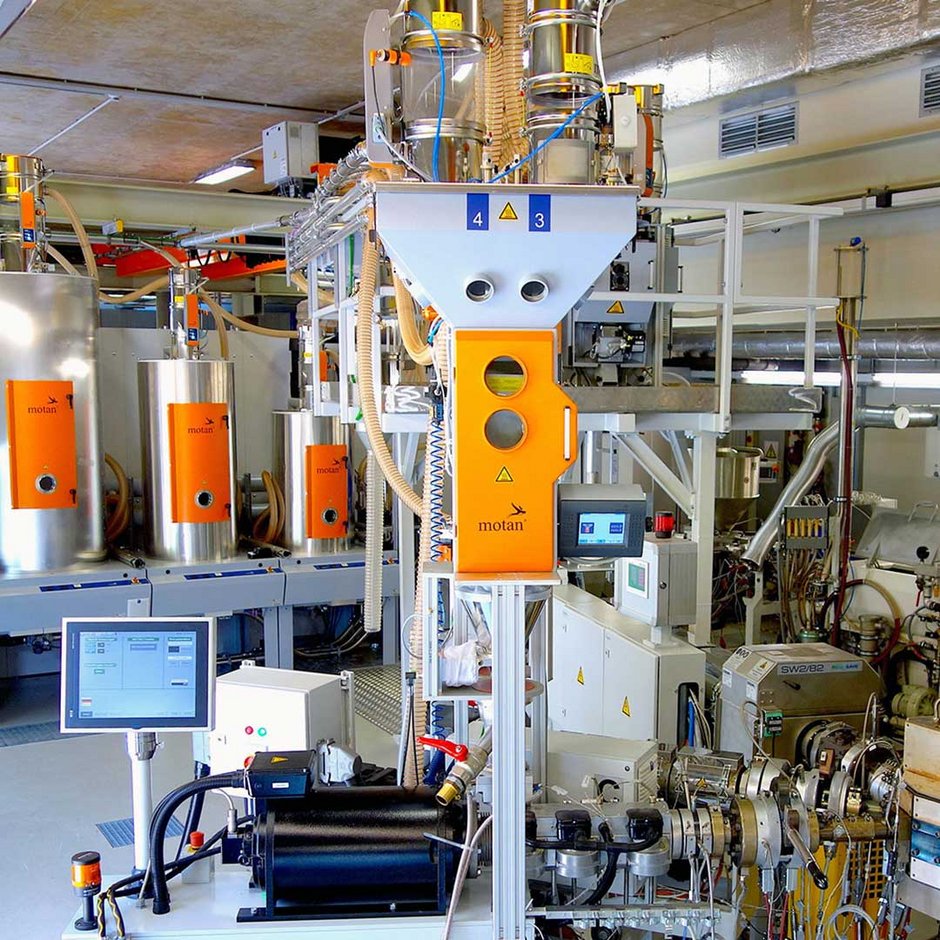
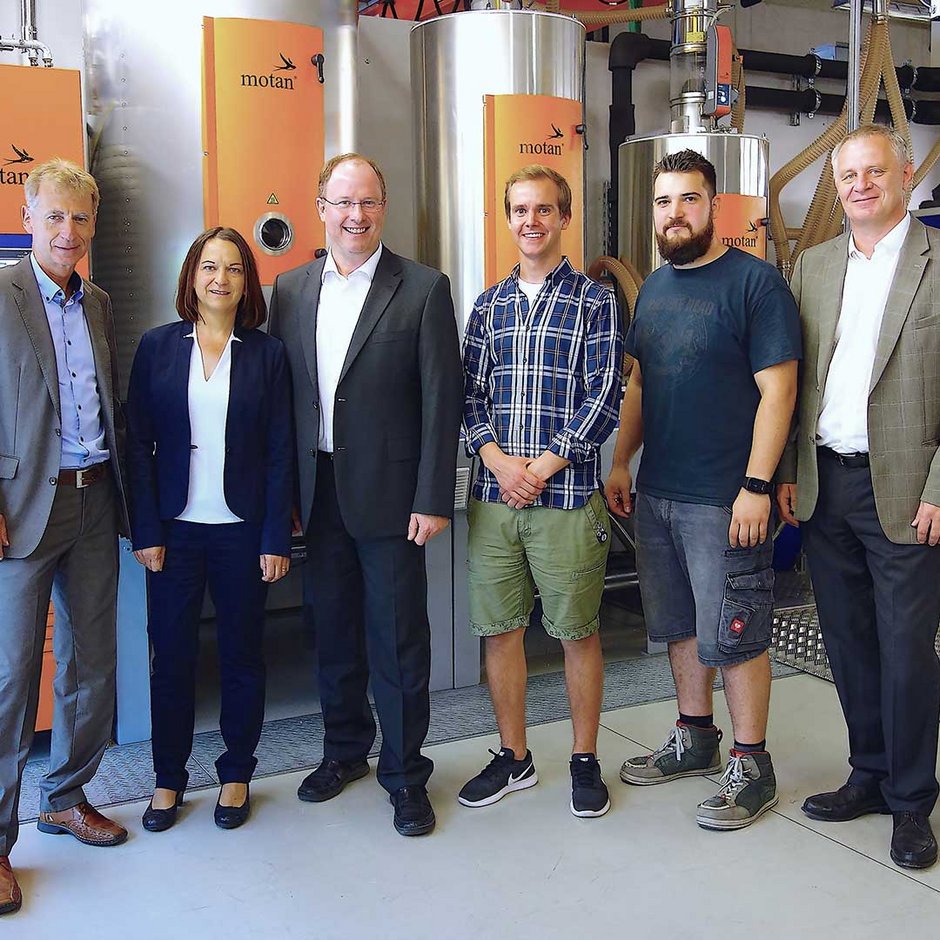
Eine über alle Komponenten durchgängig automatisierte Prozessregelung von Extrusionanlagen steht ganz oben auf der Agenda des Instituts für Polymer Extrusion und Compounding (IPEC) an der Johannes-Kepler-Universität (JKU) in Linz an der Donau. Die dafür notwendigen Regelalgorithmen werden zusammen mit Industriepartnern und weiteren JKU-Instituten aus den Fachbereichen Mechatronik und Informatik entwickelt. Entwicklungsplattform ist eine 9-Schicht-Extrusionsanlage im Industriemaßstab. motan ist als Partner mit dabei. Ziel der Zusammenarbeit ist die Entwicklung eines Easy-to-use-Anlagen-Regelsystems, in dem alle Komponenten nach Industrie 4.0 Standard miteinander kommunizieren und sich automatisch aufeinander abstimmen.
Den optimalen Betriebspunkt einer Extrusionsanlage zu finden, ist trotz der mittlerweile sehr weitreichenden Möglichkeiten bei der Sensorik und Messtechnik, der Datenverarbeitung und der Regelungstechnik immer noch eine anspruchsvolle Aufgabe für den Maschinenbediener. Insbesondere dann, wenn in Abhängigkeit von der Basismaschine auch die Betriebspunkte von so unterschiedlichen Infrastrukturanlagen, wie bspw. der Materialförder- und –dosieranlagen verändert werden müssen. Und dies besonders, wenn Produkte unter Zeitdruck häufig gewechselt werden.
Hier setzen die Forscher, Techniker und Studenten vom IPEC der JKU in Linz an. Dazu Prof. Dr. Jürgen Miethlinger: „Unsere Vision ist die selbstoptimierende Gesamtanlage, die bei einer Produktumstellung sämtliche Anlagenkomponenten zum neuen Betriebspunkt „mitnimmt“ und anschließend während des laufenden Betriebs stetig aufeinander abstimmt und optimiert. Voraussetzung dafür ist, ein präzises Abbild der Produktionsrealität vor sich zu haben. Dafür erfassen wir im Millisekunden-Rhythmus Messsignale aus allen Anlagenkomponenten. Unsere „Big Data“-Spezialisten strukturieren diese Daten, die die digitale Realität der theoretischen physikalischen Prozesse darstellen.
Am Ende des Projektes
Am Ende des Projektes werden wir eine vollständige digitale Abbildung der Gesamtanlage inklusive aller Infrastruktureinrichtungen erhalten. Unser Ziel ist es, die digitale Realmaschine als Prozesssimulator zu betreiben und mit Selbstlernfähigkeit zu ergänzen. Neue Betriebszustände können somit bereits im Voraus in allen Details simuliert und optimiert werden, sowie Regelalgorithmen für den laufenden Betrieb. Lange Produktwechselzeiten und Anlaufphasen werden damit der Vergangenheit angehören, was die flexible Nutzung von Extrusionsanlagen erleichtern wird. Eine wichtige Voraussetzung für den Erfolg der Forschung ist, dass es uns gelingt, die Prozesse der Infrastrukturgeräte voll in den Ablauf der Basisanlage zu integrieren.“
Optimaler Gesamtprozess durch optimale Teilprozesse
Ein Teilprojekt innerhalb des großen Ganzen ist die Erforschung des gravimetrischen Dosierens sowohl von Minimal- als auch Maximalmengen. Den Stellenwert dieses Teilaspekts verdeutlicht beispielhaft die Spezifikation einer 1 mm dicken 7-Schicht-Barrierefolie. Deren zentrale Schicht aus hochwertigem Barrierematerial ist 50 μm dick (= 5 Prozent Materialanteil). Darüber liegen zwei je 25 μm dicke Haftvermittler, sowie zwei 350 μm dicken Schichten Strukturmaterial, z.B. Recyclingmaterial und je einer 100 μm dicken Deckschicht. Um eine gleichbleibende Schichtdicke zu erreichen, ist die Dosierkonstanz der Materialförderung die wichtigste Größe.
Dass die motan-Geräte die diesbezügliche Erwartungshaltung der JKU-Forscher erfüllen konnten, war die technische Grundlage zum Abschluss des Partnerschaftsvertrags mit der IPEC/JKU. In einem nächsten Schritt wird die Partnerschaft auch auf die im Bau befindliche Zukunftsfabrik auf dem Universitäts-Campus – der LIT Factory – übertragen. Dort soll auf Industrie 4.0 Niveau Extrusion und Spritzguss betrieben werden.