Le savoir-faire en matière de définition de projets comme avantage face à la concurrence
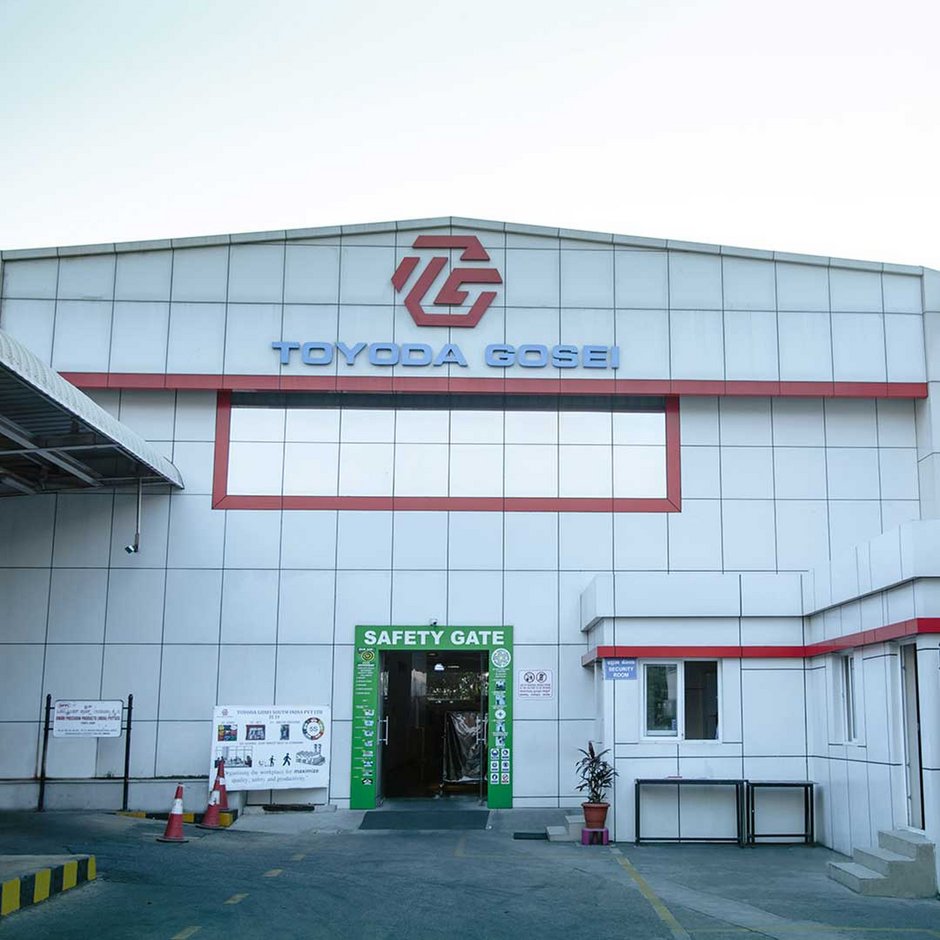
« Aujourd’hui, nous nous sommes développés pour devenir un des leaders de l’industrie automobile en Inde avec des clients comme Toyota, Nissan ou Renault », raconte Bijay Krishna Shrestha, président de la direction et directeur. Aujourd’hui, TGSIN ermploie 850 personnes environ et a réalisé l’an dernier un chiffre d’affaires de 43 millions d’euros environ.
À Bengaluru, dans le Techno Parc de Toyota, TGSIN dispose d’une surface de production de 23 400 m² environ. Ses principales tâches de fabrication comprennent le moulage par injection (intérieur et extérieur), la peinture résine (intérieur et extérieur) et les pièces de systèmes de sécurité (airbags – airbags de conducteur et de passager). L’entreprise possède plus de 25 machines de moulage à injection avec des forces de fermeture comprises entre 80 et 3 500 tonnes. Pare-chocs, grilles de radiateurs, enjoliveurs, revêtement intérieur des portes (pièces extérieures) et tableaux de bord, pièces des montants, modules de consoles et accoudoirs (pièces intérieures) sont compris dans le profil de produits.
Dans le cadre d’un élargissement de sa production en 2014, TGSIN a cherché un fournisseur pour une installation d’assèchement et de convoyage d’un part local et d’autre part proposant des solutions techniques de qualité supérieure répondant aux exigences de qualité élevées de la société. L’entreprise a trouvé ce dont elle avait besoin chez motan-colortronic Inde.
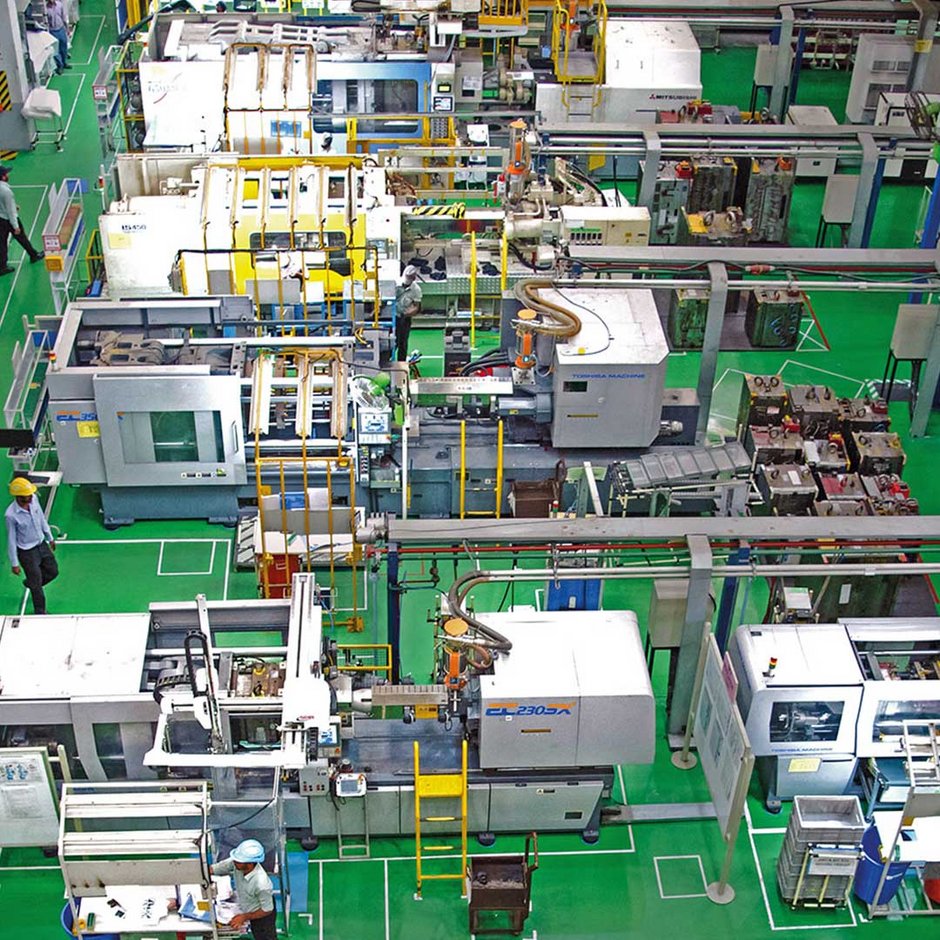
« Pour sa production, TGSIN misait sur le principe cellulaire à petites pièces, c’est-à-dire que chaque machine de façonnage a sa propre alimentation ce que beaucoup de sociétés japonaises préfèrent » explique le chef des ventes Anandakumar Ramachandran. « En 2010, l’entreprise nous a acheté 6 séchoirs à air chaud LUXOR HD 250 et 6 convoyeurs METRO HPE 06 avec le même concept » raconte-t-il sur les débuts.
Le principe cellulaire avec son alimentation en matériaux directement raccordée à la machine de façonnage présente cependant certains inconvénients comme par exemple le bruit, la chaleur, la poussière, le manque de place et les résidus de granulés dans l’entourage proche de la machine. « C’est pourquoi, lors de la deuxième phase d’extension axée sur neuf machines de moulage à injection, nous avons proposé à TGSIN un système d’assèchement et de convoyage centralisé qui se distingue tout particulièrement par une meilleure efficience énergétique en plus de l’économie de place dans la production et de la propreté tout autour de la machine de moulage à injection. Nous avons ainsi pu nous différencier nettement de la concurrence » raconte M. Ramachandran.
Une plateforme a été installée pour la nouvelle alimentation centrale en matériaux. En commençant pas l’arrivée des matériaux, on y trouve également l’installation d’assèchement et une partie du convoyage. Ces machines sont alimentées avec de la marchandise en sacs de 25 et 750 kg et leurs sorties se trouvent juste en face de l’installation d’assèchement ce qui permet d’éviter les longs transports.
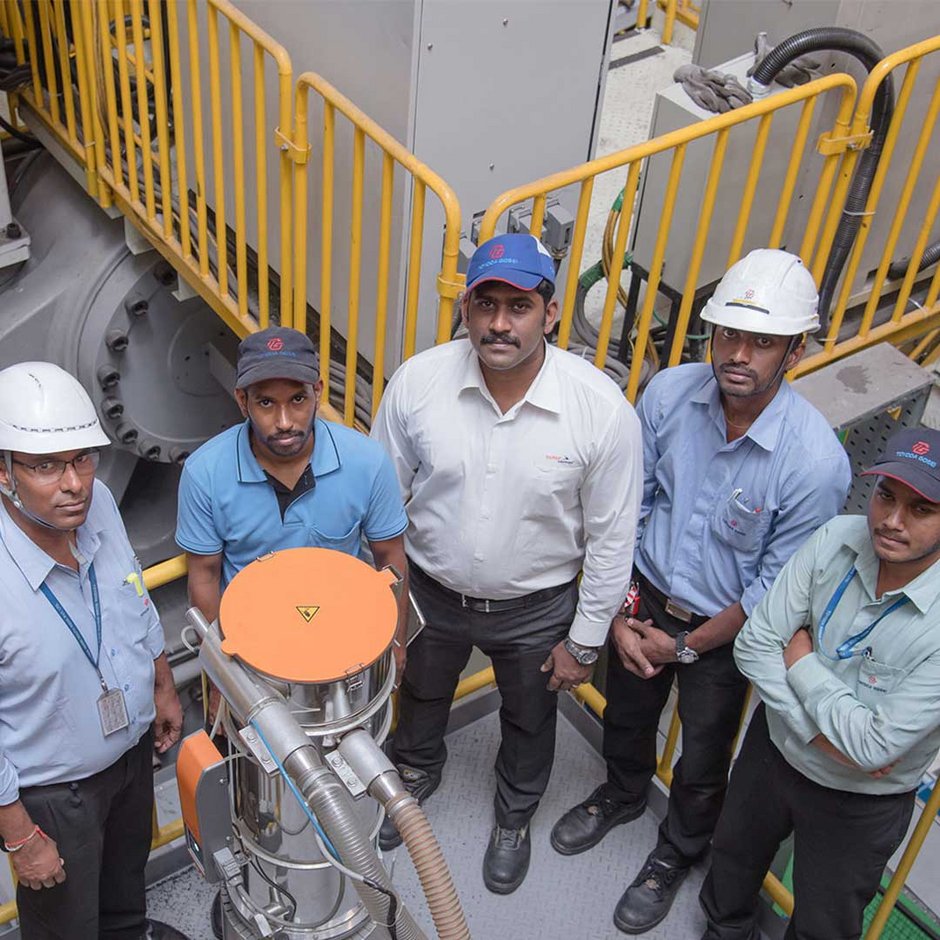
En raison de la grande variété de polymères utilisés, le convoyage central des matériaux a été conçu comme système dépendant de la machine. Cela signifie que chaque machine de moulage à injection a sa propre conduite d’entrée et que la sélection du matériau se fait au moyen d’une station d’accouplement. La table d’accouplement manuelle METROCONNECT U rend la sortie des matériaux flexible. Ainsi, plusieurs machines peuvent être raccordées à la conduite de matériau. Un autre avantage du système de convoyage centralisé est la localisation du transporteur pneumatique à un emplacement central. De cette manière, la machine de façonnage et son entourage restent dénués de salissures, de chaleur et de bruit.
Grâce à la mise en place du concept d’installation d’assèchement centralisée à la place de plusieurs dessiccateurs, la puissance d’assèchement totale consommée a été réduite de 353 kW à 159,8 kW. Ce résultat positif repose sur une combinaison intelligente de générateurs d’air et de dessicateurs de capacités en litres variés qui ont été testés et optimisés auparavant lors d’essais dans le centre technique de motan-colortronic Inde.
« motan-colortronic Inde propose des solutions et pas seulement des produits » résume M. Ramachandran. « Un de nos points forts est par ailleurs notre compétence en matière de définition de projets de élevée qui nous distingue de nos concurrents en Inde » affirme-t-il avec confiance. « Les produits que nous fabriquons en Inde présentent la même qualité que ceux venant d’Allemagne. C’est ce que nous permettent d’affirmer une recherche intensive de fournisseurs locaux capables de produits la même qualité élevée ainsi que la formation intensive de nos collaborateurs de la production.
M. Balamurugan, directeur adjoint et responsable de la maintenance des machines chez TGSIN confirme : « Nous avons choisi motan-colortronic sur les arguments de la qualité et de la fiabilité. D’autres critères étaient alors la compétence technique de l’entreprise, l’efficience énergétique élevée et des perturbations moins fréquentes. Bien que ce ne soit pas tout à fait exact. Actuellement, le nombre de perturbation s’élève à zéro. » Par ailleurs, la propreté de la production a été nettement améliorée grâce aux nouveaux appareils et aux nouvelles installations et le support du service de motan-colortronic est parfait.